LEAD Composite Current Collectors Intelligent Manufacturing Solution
As the world’s largest new energy equipment service provider, LEAD has now launched an innovative manufacturing solution for composite foils. The pioneering “magnetron sputtering + water electroplating” innovative solution effectively improves the yield rate of foils, the utilization rate of raw materials, and the equipment availability. The solution achieves significant cost savings in production and enhances differentiation competitiveness.
Program value
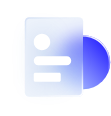
Self-developed innovative structure
significantly reduces production energy consumption and improves raw material utilization.

Efficient and stable control system
enhances coating accuracy and quality.
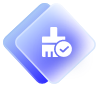
Self-innovated cleaning process
improves cleanliness of the foil surface.
Advantages of the plan
Copper composite production process path
