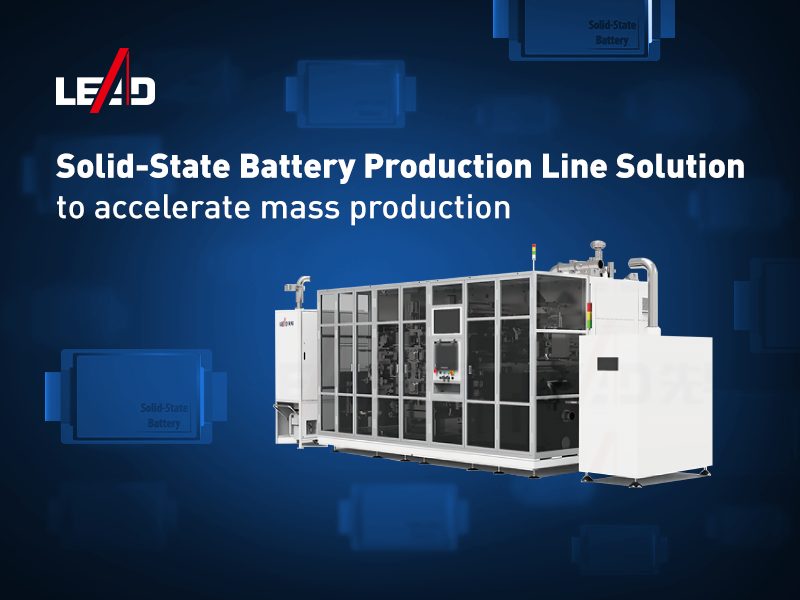
The surge in demand for electric vehicles (EVs) and energy storage systems, coupled with the acceleration of global energy transition, has driven the rapid growth of the new energy technology market, especially lithium-ion batteries. With the development of the electric vehicle industry, the demand for batteries with higher energy density, higher safety, and stronger environmental sustainability has become increasingly urgent. With the advancement of battery technology, manufacturers are seeking cost-effective and mature gigabit level production solutions to maintain competitiveness.
Solid state batteries: the forefront of next-generation battery technology
Traditional liquid lithium-ion batteries are approaching their limits and facing challenges such as limited energy density, poor low-temperature performance, and high-temperature safety risks. Solid state batteries have excellent safety, energy density, lifespan, and performance stability, making them an ideal choice for the next generation of high-performance batteries.
According to the research firm EVTank’s “White Paper on the Development of China’s Solid State Battery Industry (2024)”, the global shipment of solid-state batteries is expected to reach 614.1 GWh by 2030, with semi-solid state batteries accounting for the highest proportion, expected to account for about 10% of the overall shipment of lithium batteries, with a market size of approximately 32 billion euros. The commercialization of all solid state batteries is expected to take place around 2030, with semi-solid state batteries dominating in the short term and gradually transitioning to all solid state technology.
Since 2021, the development of solid-state batteries has been included in the national strategies of major economies such as the United States, Japan, South Korea, and the European Union. These countries aim to achieve technological breakthroughs and large-scale production by 2030, with the goal of achieving an energy density of 400 Wh/kg while prioritizing cost control. In China, the development of solid-state batteries is a key focus of the “New Energy Vehicle Industry Development Plan (2021-2035)”, which emphasizes the importance of expanding new energy storage technologies.
On a global scale, solid-state batteries have become a strategic priority, marking a critical moment in the field of new energy.
Overcoming the challenges of mass production of solid-state batteries
The mass production of solid-state batteries requires breaking through technological bottlenecks, especially for lithium battery equipment. The complex manufacturing process requires a combination of cutting-edge laboratory research and rich on-site practical experience. It is crucial to reduce costs while ensuring quality. The performance of the production line and the technical expertise of service providers are the key to balancing cost-effectiveness and high standards.
Leading Intelligent Equipment (LEAD) is a globally leading provider of intelligent manufacturing solutions for the new energy industry, recognizing the potential of solid-state batteries as early as 2018. Since then, Navigation Intelligence has invested heavily in this technology to adapt to global trends and accelerate the localization of high-end equipment. In June of this year, Leading Intelligence launched a self-developed all solid state battery production line, accelerating the global mass production process.
LEAD has identified key bottlenecks in the mass production of solid-state batteries, with a focus on the manufacturing of electrodes and electrolyte membranes, as well as densification processes. The electrochemical and physical properties of materials have a significant impact on the thickness and ionic conductivity of solid-state electrolyte membranes. The traditional wet process faces challenges such as uneven material dispersion, inconsistent membrane quality, and excessive deformation of the battery during compression, which hinder the efficient mass production of solid-state batteries.
To this end, LEAD’s R&D team took the lead in developing a groundbreaking dry electrode manufacturing technology. This method utilizes an innovative and efficient stirrer to shear mix raw materials while eliminating the use of solvents, thereby improving electrode performance. With years of experience in manufacturing rolling equipment, LEAD has developed advanced dry electrode forming and laminating technology to ensure consistent electrode quality and achieve efficient mass production. The company’s most advanced ultra-thin electrolyte membrane manufacturing and coating equipment adopts innovative components, which can significantly improve production efficiency, quality, and automation level.
At present, the main focus of solid-state battery production is prototype battery manufacturing, which usually involves single-layer or limited multi-layer design. In this case, issues such as edge collapse during compression have little impact on battery performance. However, addressing these challenges is crucial for advancing the production of all solid state batteries, as densification technology is essential for large-scale battery manufacturing. LEAD’s proprietary densification technology strikes a balance between battery performance and mass production. By integrating advanced battery insulation framework technology, LEAD’s equipment minimizes edge shear and collapse during compression, significantly improving the stability of solid-state battery mass production and reducing the risk of short circuits after densification.
Innovation to promote sustainable development in solid-state battery manufacturing
From research and development to commercialization, solid-state battery manufacturing must effectively balance yield, cost, and environmental sustainability. To meet the challenges of strict production requirements, reduce energy consumption, and improve sustainable performance, Pioneer Technology has taken the lead in innovating “unmanned, integrated, and intelligent” production lines, not only achieving equipment integration, but also prioritizing the safety of the production process.
In addition to the essential equipment covering all aspects of solid-state battery production, Pioneer Technology has also achieved seamless integration between machines, optimized overall process control and traceability. Through its own Lead ACE intelligent manufacturing turnkey solution, it provides highly automated and intelligent production line solutions for solid-state battery manufacturers. By simplifying processes, shortening production cycles, and accurately controlling microenvironments, it ensures efficient and high-quality production while significantly reducing energy consumption, labor costs, and overall investment, helping customers reduce costs, improve efficiency, achieve sustainable development, and promote the industry towards a new era of green and low-carbon production.
Pioneer Technology has successfully overcome the technical challenges of solid-state battery mass production, achieving a complete full line solution, which not only promotes the mass production of solid-state batteries, but also drives the industry into a new stage of development.
Committed to technological excellence and driving energy transformation for 20 years
The leading position of Pioneer in the field of solid-state battery manufacturing stems from 20 years of technical expertise. With a strong foundation in research and engineering, Pioneer can customize production systems according to the needs of various battery types such as lithium-ion and sodium ion batteries, providing efficient and stable production lines.
Since 2023, Pioneer Technology has collaborated with industry giants to obtain orders for the entire production line of solid-state batteries from globally renowned car manufacturers and solid-state battery companies. Key pilot equipment such as dry electrode film forming equipment, laminating machines, and soft pack assembly lines have been exported to the United States, Europe, and other places to assist customers in process development and verification. At the same time, Pioneer Technology has achieved significant results in innovative technologies such as slurry mixing, dry film forming, rolling, laminating, assembly, chemical transformation, and intelligent logistics on the world’s first solid-state battery mass production line, driving the industry to new heights.
With the maturity of solid-state battery technology, Pioneer Technology is ready to serve the high-end electric vehicle, energy storage, and consumer electronics markets. Pioneer Technology’s business covers more than 20 countries and regions, with over 5000 R&D personnel, providing one-stop services from consulting, design, installation, and future upgrades for new energy intelligent manufacturing.
The establishment of the European logistics center further strengthens LEAD’s global service network, ensuring shorter delivery times and higher efficiency for European customers. With the acceleration of commercialization of solid-state batteries, LEAD’s technological leadership will help drive the global energy transition.
LEAD helps shape the sustainable future of the electric vehicle and energy storage industries through innovative solutions, providing support for the next generation of green and low-carbon production.