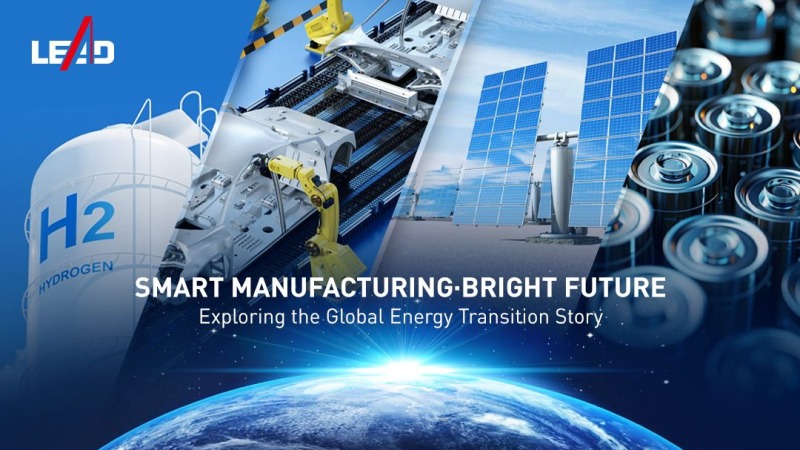
Introduction
With the rapid advancement of AI technology, its transformative potential in industrial applications is increasingly evident. Lead Intelligent Equipment (LEAD), leveraging its cutting-edge expertise in lithium battery AI and successful project implementations, partnered with a top EV and energy storage battery manufacturer to upgrade the electrolyte filling production line. This upgrade significantly enhanced both quality and efficiency, underscoring the value of AI-driven transformation.
Client Overview
The client is a leader in the EV battery and energy storage industry, renowned for launching innovative battery products recognized globally. With high production volumes and a strong reputation for technological advancement, the client sought a more efficient, precise, and stable solution for the electrolyte filling process—a critical step in lithium-ion battery production.
Challenge: The EL re-filling process relies heavily on manual intervention, leading to poor adjustment results.
Electrolyte filling, a crucial step in lithium-ion battery manufacturing, directly affects the performance, safety, and efficiency of the cells.
In production, issues such as early technological limitations, equipment aging, and environmental influences can lead to blockages, crystallization, and leaks in the filling pipes, resulting in deviations in filling volume over time. Traditionally, manual adjustments and EL re-filling are used to correct non-conforming (NG) products. However, manual intervention is often delayed, relies on operator experience, and lacks standardization, leading to lengthy calibration processes and subpar adjustment results.
With high production volumes and stringent demands for battery performance, the client urgently needed to enhance its electrolyte re-filling capabilities. After numerous unsuccessful attempts to meet expectations through traditional methods, it became clear that these methods could no longer satisfy the market’s increasing requirements for precision, speed, and stability. The industry needed a more precise, efficient, and reliable automated electrolyte re-filling solution.
Upon learning that LEAD could upgrade production lines using AI technology, the company partnered with LEAD for an intelligent overhaul of its electrolyte filling and compensation line—aiming to leverage AI to overcome the challenges of electrolyte filling control and boost competitiveness.
LEAD´s Solution: AI-Powered Targeted Upgrade for Enhanced Production Quality and Efficiency
After evaluating LEAD’s capability to elevate production lines through AI, the client collaborated with LEAD to upgrade their electrolyte filling and compensation processes. The aim was to introduce AI to minimize manual intervention, increase efficiency, improve quality, and ultimately reinforce the client’s market position.
An in-depth analysis revealed numerous dynamic factors affecting EL re-filling volume. The gradual changes in volume over time make it challenging to precisely determine the appropriate compensation. AI technology, with its self-learning and self-adaptive capabilities, presented the ideal solution.
LEADACE, an advanced AI platform, was employed to monitor critical points, accurately determine re-filling volumes, and issue prompt adjustment instructions—leading to consistent, high-quality results.
By adopting LEADACE, the AI platform precisely identified critical nodes of abnormalities, calculated electrolyte re-filling volume, and issued timely adjustment instructions. This rapid, flexible solution minimized human intervention, maximizing both production efficiency and product quality. The innovative upgrade quickly delivered excellent results, fully meeting the client’s expectations.
Impact of the Upgrade
Intelligent Perception Leads to Defective Products Reduction
The solution, equipped with the LEADACE platform, enabled real-time monitoring and adjustments, significantly reducing manual intervention and defective products. Customer data revealed that NG battery cells per upgraded machine dropped by 47 units daily. With four machines on a production line, yield improvements ranged from 0.01% to 0.1%, while older lines typically saw gains from 0.1% to 2.5%.
Precise Control Reduces Production Losses
By deeply integrating AI to automate and precisely control dispensing parameters, production losses at the electrolyte filling stage were significantly reduced. Data showed that a production line with four new filling machines saved approximately 4.75 tons of electrolyte annually, resulting in direct economic savings of 49,000 euros.
Exclusive Platform Boosts Efficiency
The AI-powered platform created a tailored data environment that evolved over time, improving analysis accuracy and multidimensional capabilities. This led to smoother workflows, faster response times, and enhanced problem-solving efficiency. Feedback from the client indicated that their team’s decision-making efficiency improved significantly due to these advancements.
Dual Enhancements and Deepened Applications
Soon after deployment, the AI-powered system achieved a closed-loop electrolyte filling yield of 99.98%, marking a substantial improvement in both production efficiency and economic benefits. The successful implementation underscored the vast potential of AI to optimize production quality and cost-efficiency. The client affirmed LEAD’s technical acumen and ability to execute targeted upgrades effectively. The project leader noted, “The LEAD team has deep technical knowledge and extensive project experience, allowing them to swiftly identify root causes and implement targeted, effective solutions to overcome challenges during the upgrade.”
About LEAD
Lead Intelligent Equipment (LEAD), a private company established in 1999, is one of the world’s largest suppliers of new energy manufacturing equipment. LEAD specializes in designing, engineering, and constructing advanced manufacturing solutions for leading global lithium battery manufacturers and OEMs in the automotive, renewable energy, and technology sectors. LEAD provides professional, personalized, and customized services to its clients worldwide.
Today, LEAD is a globally trusted provider, partnering with industry leaders to scale up lithium battery production in Europe, contributing significantly to the global transition towards clean energy.