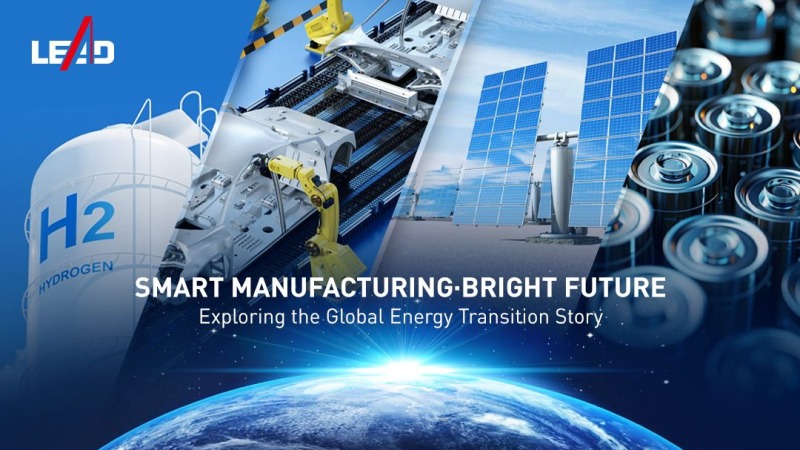
With the rapid advancement of AI technology, its algorithmic and analytical advantages in industrial applications are increasingly evident. Lead Intelligent Equipment (hereafter referred to as LEAD), leveraging cutting-edge research in lithium-ion battery AI and the implementation of several landmark projects, has gained high recognition from a leading client in the lithium-ion battery sector for upgrading their electrolyte filling compensation line with AI technology.
This client has achieved remarkable success in the fields of power battery and energy storage battery, launching various battery products based on different technological pathways. Their products are highly acclaimed in various niche markets, with their technology, product quality, and production volume far ahead on a global scale.
Overreliance on Manual Intervention in Electrolyte Filling with Suboptimal Effects
As a critical step in the lithium-ion battery manufacturing process, the quality of electrolyte filling directly impacts battery performance, safety, and production efficiency. Consequently, the electrolyte filling phase demands high precision, speed, stability, and automation of process equipment.
However, in actual production, factors such as early-stage process limitations, equipment aging, and environment can lead to inevitable issues like blocked filling pipes, electrolyte crystallization, and leaks after a certain period of operation. Consequently, the filling volume deviates from the initial standards. Traditionally, manual adjustments and compensation have been employed to eliminate non-conformities (NG). Yet, manual intervention often lacks timeliness, and compensation amounts are reliant on production experience, making standardization difficult and prolonging calibration time with poor adjustment outcomes.
Due to the immense production volume and high demands for battery performance and efficiency, this client has a pressing need to enhance their electrolyte filling compensation capabilities. After several unsuccessful attempts at improvement, they realized that traditional compensation methods no longer meet the rapidly evolving market demands in terms of production accuracy, response speed, and product stability. The industry urgently requires a more accurate, efficient, and reliable automated electrolyte filling compensation solution.
Upon learning that LEAD could enhance the intelligence of their production line through AI technology, thereby overcoming equipment limitations, the client collaborated with LEAD to smartly upgrade their electrolyte filling compensation line, seeking solutions to the compensation challenges in this process.
Tailored AI Smart Upgrade Plan, Enhancing Production Quality and Efficiency
The goal of this project is to introduce AI technology for the intelligent upgrade of electrolyte filling nodes, reducing manual intervention and achieving significant improvements in production efficiency and product quality, while also enhancing first-pass yield and reducing production costs, thereby bolstering the company’s market competitiveness.
In-depth analysis by both parties revealed many dynamic factors affecting electrolyte filling compensation amounts, and that changes in filling volume occur gradually over time, making it difficult to mechanically define compensation amounts. AI technology, with its inherent advantages of self-learning and self-upgrading, is ideally suited to tackle this challenge.
By utilizing the LEADACE intelligent platform, AI technology identifies key nodes for abnormal occurrences, accurately calculates filling compensation amounts, and promptly issues adjustment instructions. This approach offers rapid response, high flexibility, and eliminates the need for manual operation, significantly reducing the impact of manual intervention on the production line, and notably improving production efficiency and product quality.
This innovative upgrade plan quickly gained client approval and achieved excellent results following deployment, successfully meeting client expectations.
Intelligent Prediction to Reduce NG
The solution features LEAD’s latest LEADACE AI platform, which monitors the production process in real-time and promptly identifies and corrects anomalies, leading to a noticeable reduction in manual operations and NG rates. Client feedback indicates that the upgraded equipment reduced the average daily NG cell count by 47 per machine. With four filling machines on a production line, the revamped equipment production line can enhance yield by approximately 0.01% to 0.1%, while the traditional equipment line can see yield improvements of 0.1% to 2.5%.
Precise Control to Reduce Waste
Simultaneously, the deep integration of automation and intelligence has optimized the production process at the electrolyte filling node. By enabling automated and precise control of input parameters through the AI system, production waste has been significantly reduced. Actual operating data shows that a production line equipped with four new filling machines can save approximately 4.752 tons of electrolyte annually, yielding direct economic benefits of about $52,000.
Exclusive Platform to Enhance Efficiency
Furthermore, because the AI system establishes a data environment unique to the client, it will self-develop and correct over time, resulting in more objective data analysis, multifaceted functionality, and more reliable outcomes. This helps the client quickly identify issues and improve the accuracy of production management. Client feedback indicates that with the assistance of AI data analysis, their team’s response speed, problem-solving abilities, and decision-making efficiency have all improved, leading to a smoother and more efficient overall workflow.
This embedded upgrade has quickly demonstrated significant improvements in precise control and intelligent prediction, achieving a closed-loop yield rate of 99.98% for electrolyte filling, and directly enhancing the client’s production efficiency and economic benefits.
Recognizing the substantial results of this upgrade project, the client acknowledges the immense potential of AI technology in enhancing production efficiency and optimizing cost structures, as well as gaining deeper insight into LEAD’s technical prowess in the field of intelligent battery manufacturing.
The project leader remarked, “The LEAD team possesses deep technical expertise and extensive project experience, enabling them to accurately pinpoint the root causes of problems and propose and implement targeted solutions that effectively resolve technical challenges encountered during the upgrade process.”
Looking ahead, LEAD will continue to enhance AI algorithms and models, improving the flexibility and emergency response capabilities of the LEADACE platform under extreme conditions, delivering an unparalleled experience in production efficiency and product quality enhancement for clients.
Currently, digitization based on big data and cloud computing, along with the industrial internet, is becoming the development direction of the manufacturing industry, which is seeking a rapid and stable digital transformation path tailored to its needs. While providing intelligent equipment, LEAD also utilizes IoT, big data, AI, and edge computing technologies to build the LEADACE intelligent manufacturing system, offering clients a closed-loop information solution. This flexible configuration can achieve standardized and intelligent management across the entire process—from raw materials, planning, production, packaging, to delivery—enabling managers to accurately and promptly grasp the real-time status of the factory, helping manufacturing enterprises improve operational efficiency, shorten delivery times, and reduce costs, and facilitating the realization of digital and intelligent factories.