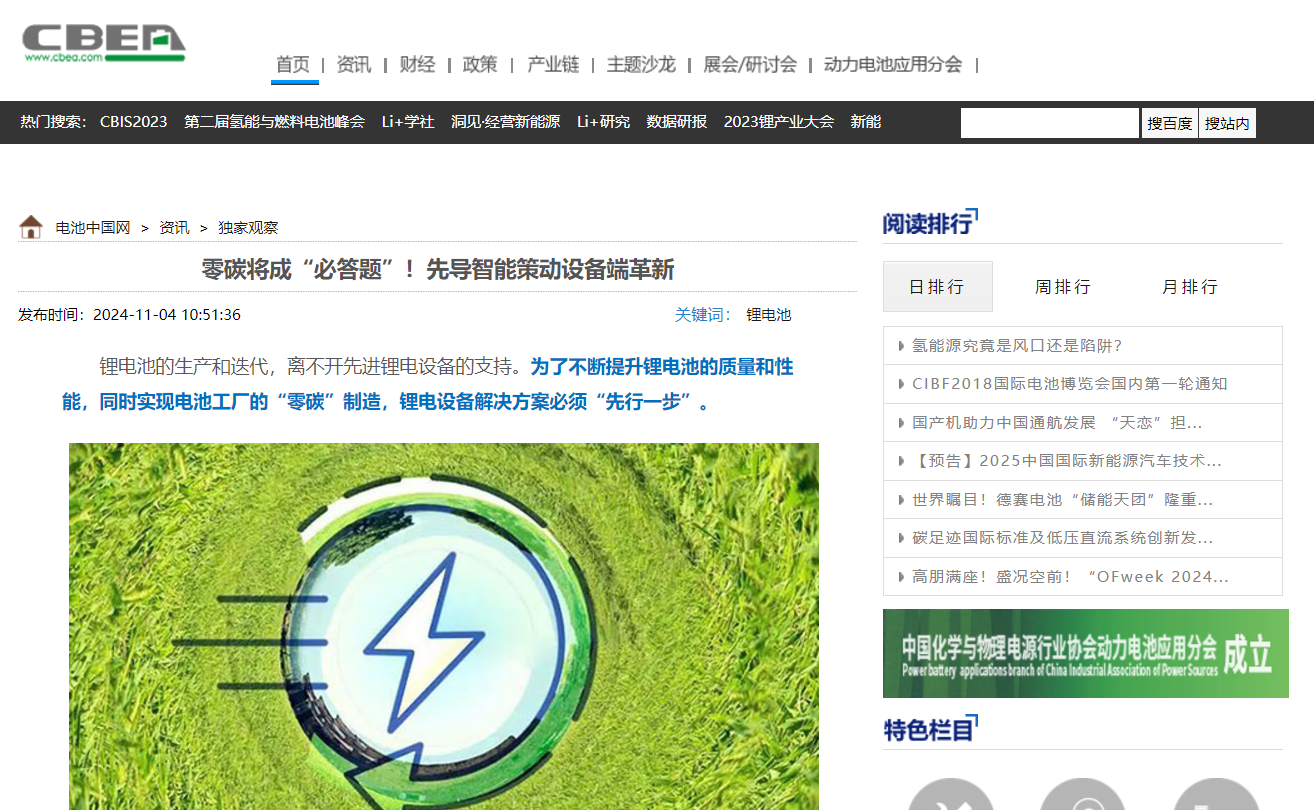
On November 2, CBEA published an opinionby journalist Huang Li titled “Zero Carbon: A Must-Answer Question! LEAD Drives Innovation in Battery Manufacturing Solutions.”
The evolution of lithium-ion battery production and technology hinges on advanced manufacturing equipment. To consistently improve battery quality and performance while achieving “zero carbon” production in battery plants, equipment solutions must remain at the forefront of innovation.
In recent years, China’s lithium-ion battery equipment sector has seen continuous upgrades, providing robust support for the country’s leading position in global battery installations. Equipment manufacturers have also helped battery enterprises develop new battery technologies, establish zero-carbon facilities, and overcome numerous technical challenges.
Currently, all-solid-state batteries are emerging as a key focus for next-generation battery technology due to their high energy density, long lifespan, and superior safety. Leading global battery enterprises are actively investing in R&D to address challenges like high interfacial resistance and demanding manufacturing processes, aiming to accelerate the commercialization of all-solid-state batteries.
Globally, over 150 countries have announced carbon neutrality targets, reflecting strong commitment and action toward zero-carbon transitions. The emphasis on environmental protection and sustainability in many countries has become a key driver of demand for zero-carbon factories. Leading battery manufacturers, including CATL, Envision AESC, EVE Energy, Gotion High-Tech, SVOLT, Farasis Energy, Sunwoda, and REPT, have already built or are actively pursuing zero-carbon battery facilities. As global decarbonization efforts intensify and technology advances, zero-carbon factories are set to become a mainstream trend in the lithium-ion battery industry.
Against this backdrop, lithium-ion battery equipment solutions are entering a new wave of innovation. Leading manufacturers are ramping up R&D for solid-state and all-solid-state battery equipment, forming close collaborations with battery enterprises to accelerate the commercialization of these technologies.
LEAD Secures All-Solid-State Battery Production Line Orders
Market dynamics indicate that enterprises capable of mass-producing automotive all-solid-state batteries will gain a first-mover advantage. Innovation in battery manufacturing equipment is a critical enabler in this race.
As a global leader in smart manufacturing solutions for the new energy industry, Lead Intelligent Equipment (hereafter referred to as LEAD) announced recent breakthroughs in the solid-state battery domain. Since 2023, LEAD has partnered with multiple industry leaders and secured domestic and international orders for all-solid-state battery production lines, attracting significant industry attention.
LEAD has successfully developed end-to-end solutions for all-solid-state battery production, covering key processes such as electrode production, coating and lamination, stacking, cell assembly, formation and aging, and logistics. These innovations have been deployed on mass-production lines for downstream clients. LEAD also noted that it will continue collaborating with partners to advance the industrialization of solid-state batteries.
This achievement highlights LEAD’s significant breakthroughs in solid-state and all-solid-state battery technologies and underscores its forward-looking innovation in the new energy sector.
In October, LEAD’s all-solid-state battery production line solutions were a major highlight at the Battery Show in India and the U.S., garnering attention from professionals and industry experts. This reflects rising interest in solid-state battery equipment solutions and LEAD’s leadership in technological innovation and application.
With the successful delivery of its mass-production solid-state battery projects, LEAD’s equipment solutions have earned client recognition. Its dry electrode coating and solid electrolyte production technologies are now among the industry’s most advanced.
Notably, LEAD’s all-solid-state dry electrode equipment reduces labor requirements by 20% and investment costs by 30% through process simplification and intelligent control, enabling clients to quickly capture market opportunities.
As solid-state battery technology progresses and commercialization accelerates, LEAD is poised to provide advanced manufacturing solutions for markets such as consumer electronics, premium electric vehicles, and energy storage.
“Full Value Chain + Full Lifecycle” Low-Carbon Smart Manufacturing Solutions
Mass production of solid-state batteries relies on overcoming core technical challenges in manufacturing equipment.
As countries pursue “dual carbon” goals, global automakers are accelerating the transition to electrification and low-carbon production. This raises the bar for battery enterprises in energy efficiency and carbon reduction, driving demand for zero-carbon lithium-ion battery plants.
However, constructing low-carbon factories presents several challenges:
Technical Barriers: Achieving low-carbon emissions requires advanced energy-efficient technologies and effective use of renewable energy, which face cost, efficiency, and stability constraints.
Complex Processes: Designing and building low-carbon factories involves multifaceted considerations, from energy use to waste reduction and recycling, making the process lengthy and intricate.
High Initial Investment: Equipment upgrades, technology adoption, and energy system overhauls pose significant financial pressures on enterprises.
Unproven Economic Returns: Uncertainties remain around the carbon reduction potential of low-carbon factories and their compliance with overseas carbon footprint standards.
As a committed enabler of sustainable development in the new energy industry, LEAD has introduced “Full Value Chain + Full Lifecycle” low-carbon smart manufacturing solutions, offering critical support for global green and low-carbon initiatives.
Leveraging proprietary innovations, LEAD helps clients optimize energy use and reduce emissions throughout the production lifecycle. This includes precision control of microenvironments, efficient management of compressed air, and real-time energy monitoring to achieve comprehensive carbon reduction.
Through its platform strategy, LEAD has expanded beyond lithium-ion and photovoltaic equipment manufacturing into hydrogen energy, energy storage, and electric vehicles, constructing a holistic green manufacturing ecosystem for new energy sectors worldwide.
To date, LEAD’s smart equipment has served over 20 countries and regions, supporting global energy-saving and emission-reduction efforts. Its innovations continue to reduce energy consumption and emissions during both equipment production and client operations.
As the global push for carbon neutrality accelerates, the race to industrialize next-generation batteries, led by all-solid-state batteries, will drive further innovation in battery manufacturing equipment. Simultaneously, the adoption of smart low-carbon factories in energy-intensive industries will expand, advancing the vision of a sustainable future.