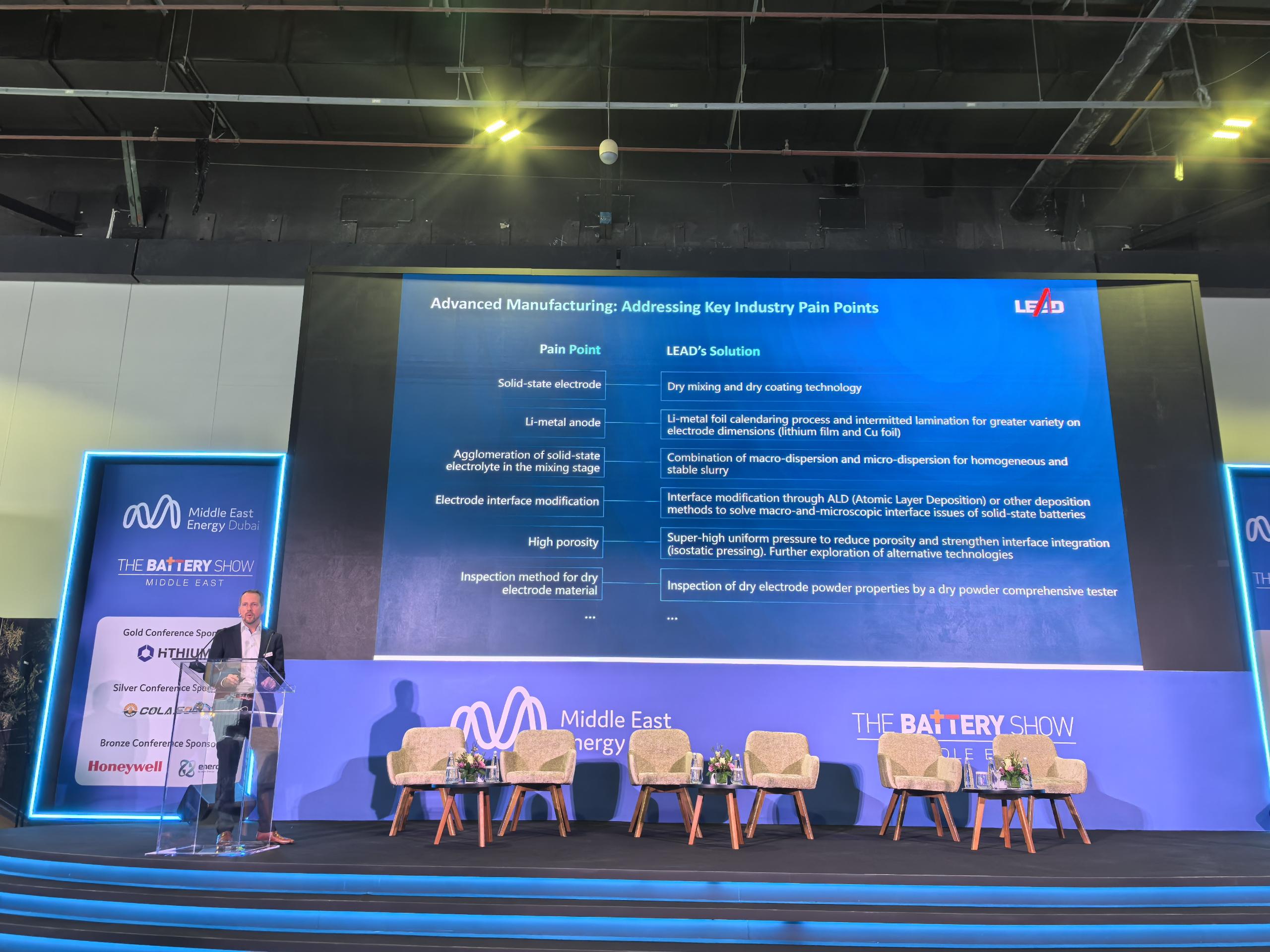
Module Turnkey Solutions for Automotive Manufacturing
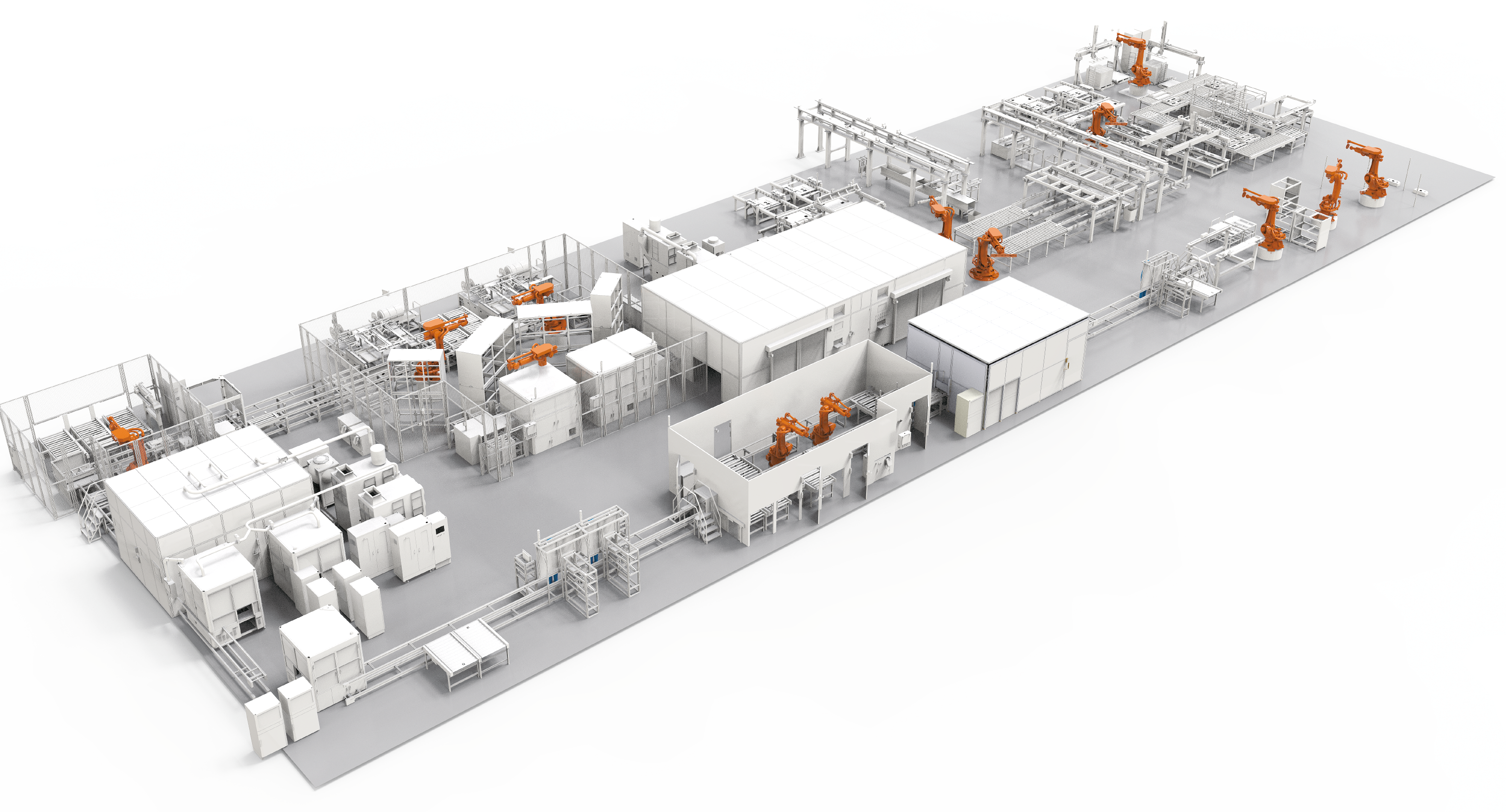
As a global leader in battery equipment manufacturing, LEAD offers a comprehensive suite of services tailored to lithium battery module production. Our services cover factory planning, consultancy, specialized machinery, custom MES, assembly line integration, intelligent logistics warehousing, and module disassembly for various types of production lines including prismatic cells, cylindrical cells, large cylindrical cells, and pouch cells.
Our module line solution encompasses key processes such as cell auto loading and code scanning, cell plasma cleaning, cell AB gluing, cell stacking, laser welding, CCD positioning, and EOL testing. Integrated with LEAD’s proprietary intelligent logistics system and MES system, our production line consistently achieves an overall yield rate exceeding 99% and an availability rate exceeding 95%.