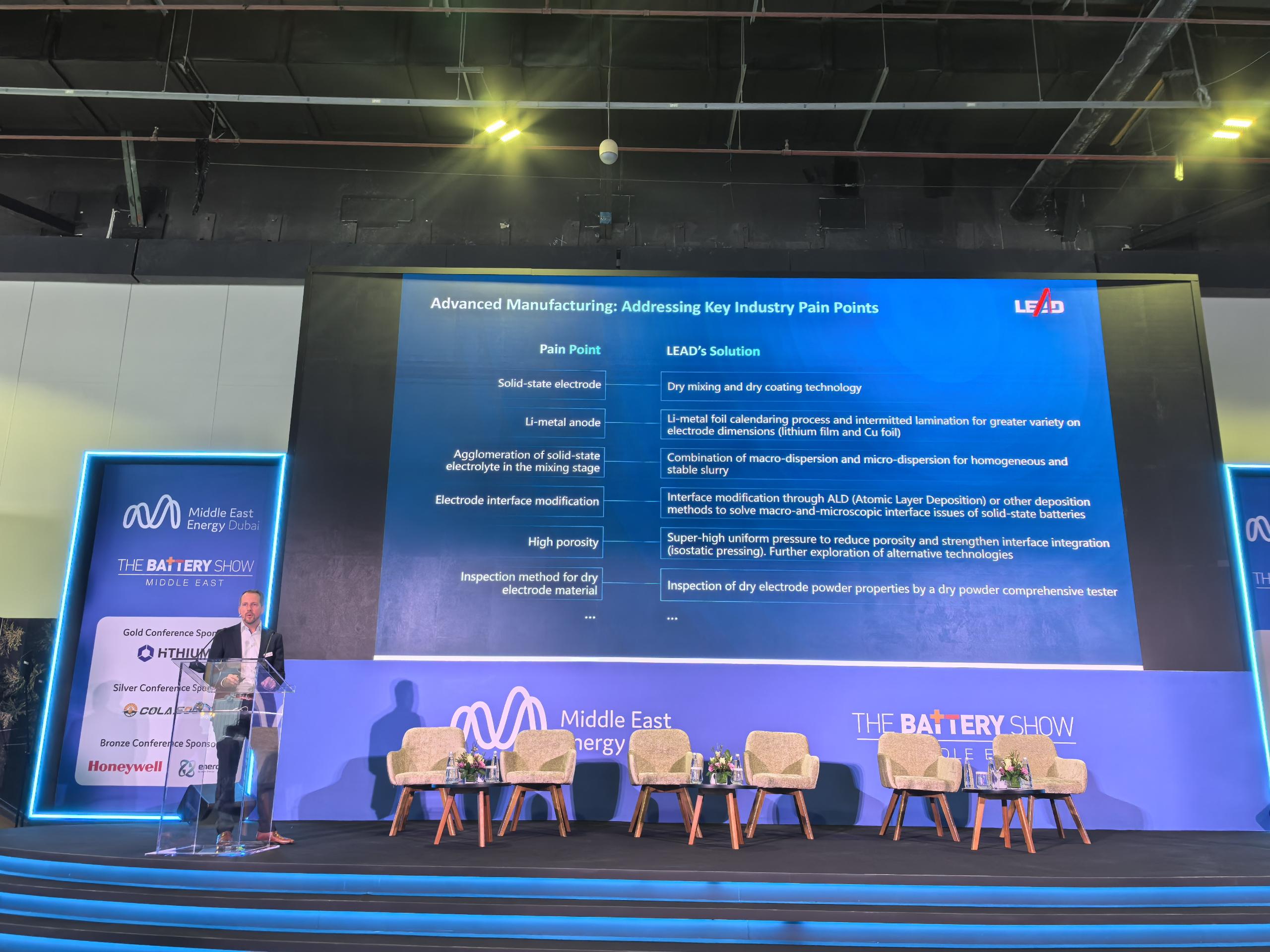
Prismatic Battery Turnkey Solutions for Li-Ion Battery Manufacturing
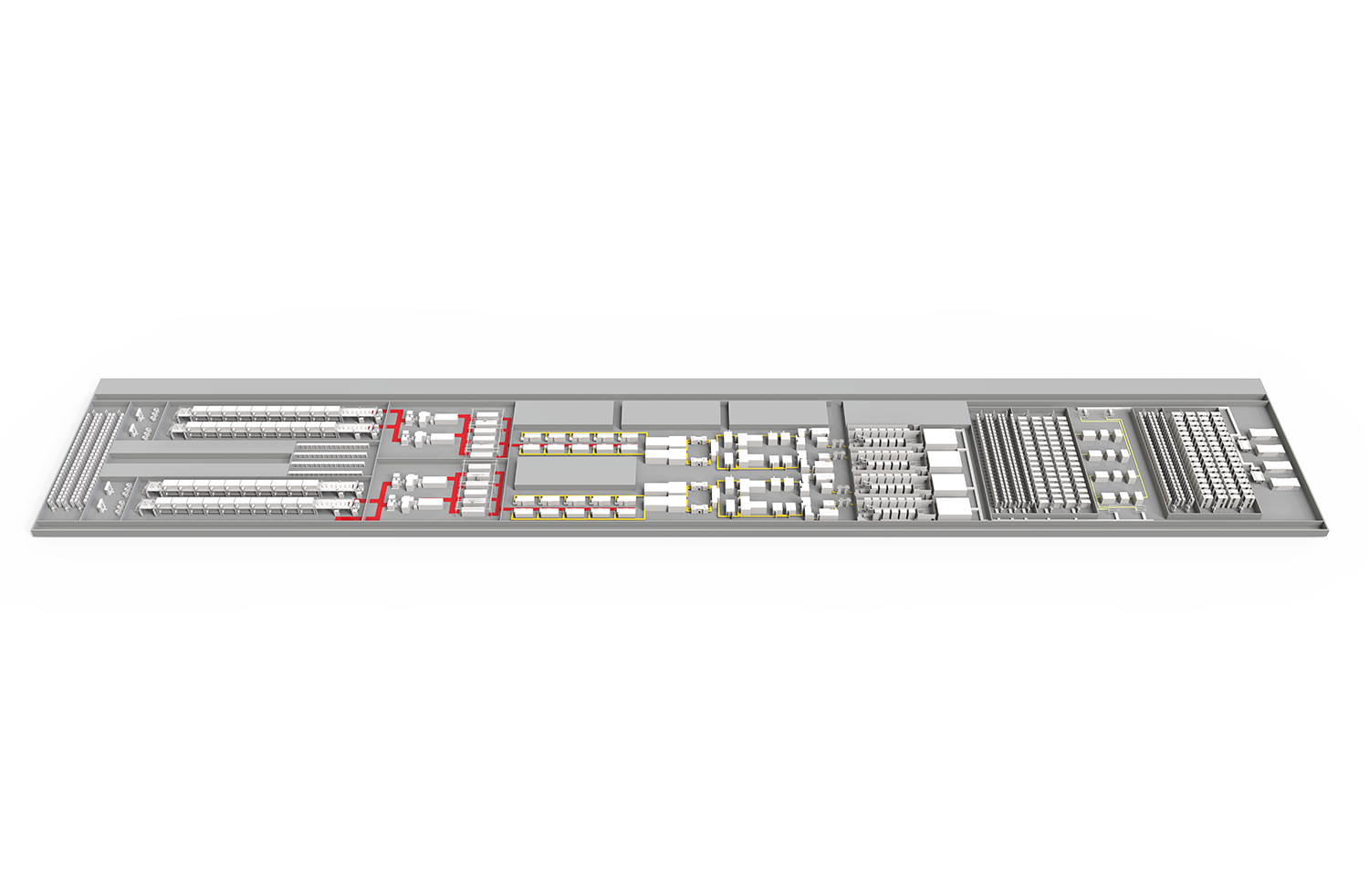
As the world’s largest Li-ion battery intelligent manufacturing turnkey solution provider, we provide turnkey solutions for prismatic cell, pouch cell, cylindrical cell, sodium-ion cell and solid-state cell, and have the highest market share in the EV cell and energy storage cell. At present, we have established strategic partnerships with many well-known cell makers around the world.
We cover end-to-end equipment, that the giga factory needs. Give consult to the customers to build their plant in a short time, which mean they will realize to produce quickly. We have abundant experience of the whole, we provide 100+ lines to the customers. We are also the only Li-ion battery whole line service provider with 100% independent intellectual property
rights worldwide.
The whole line @prismatic covers electrode making, assembly, and formation & aging process. We provide Li-ion battery whole line equipment from mixing, coating, calendering, slitting, winding/stacking, cell assembly, formation and aging, as well as intelligent logistics that runs through the whole line. Together with the self-developed MES, we dedicate to build an intelligent factory for Li-ion battery enterprises.
As Li-ion battery manufacturing continues to develop towards complete automation, information-based and intelligent direction, the equipment we provide will also be developed from individual equipment to segmented integrated equipment, and then to full life cycle whole line solutions.