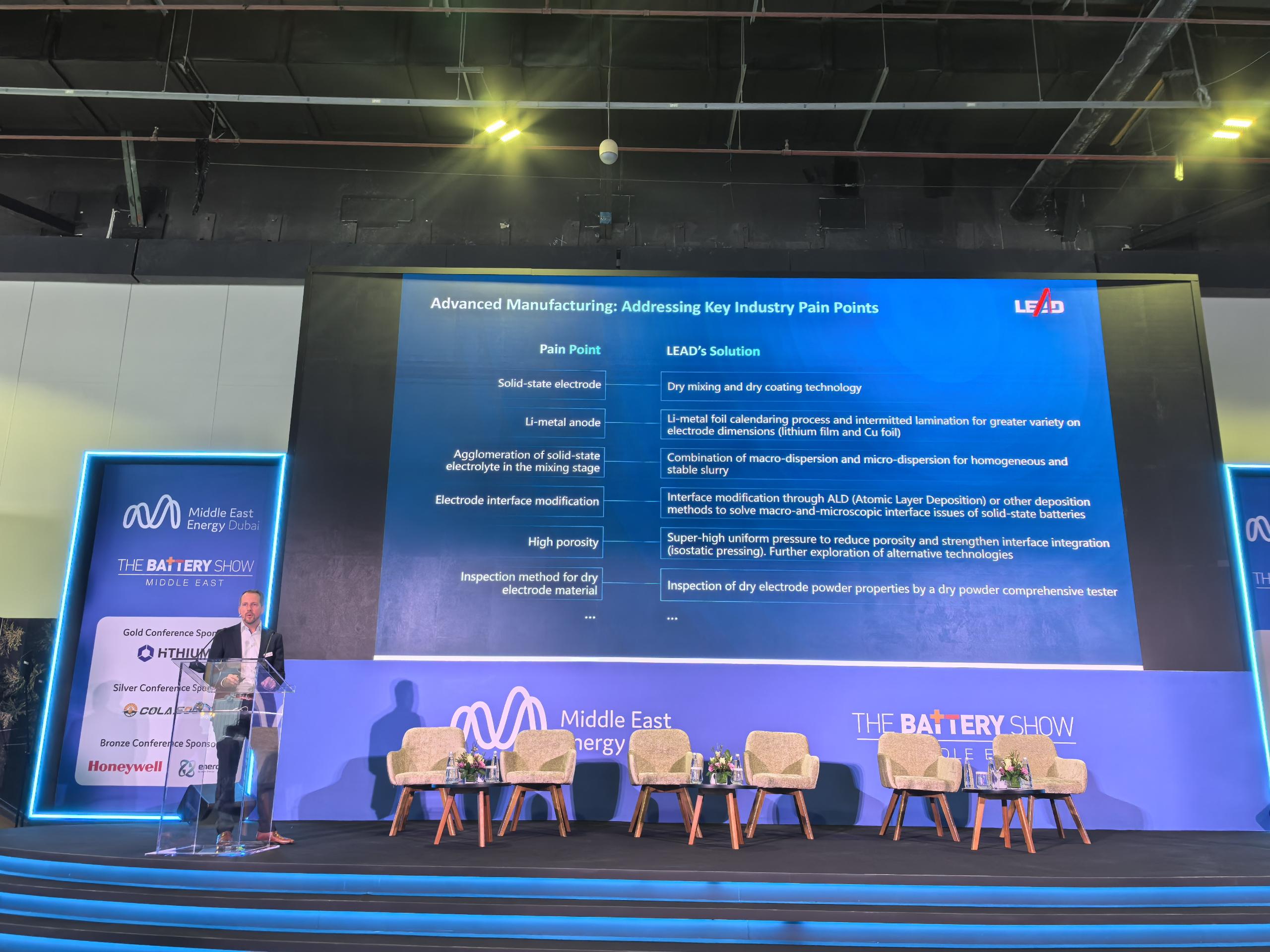
Solutions for PV module intelligent manufacturing
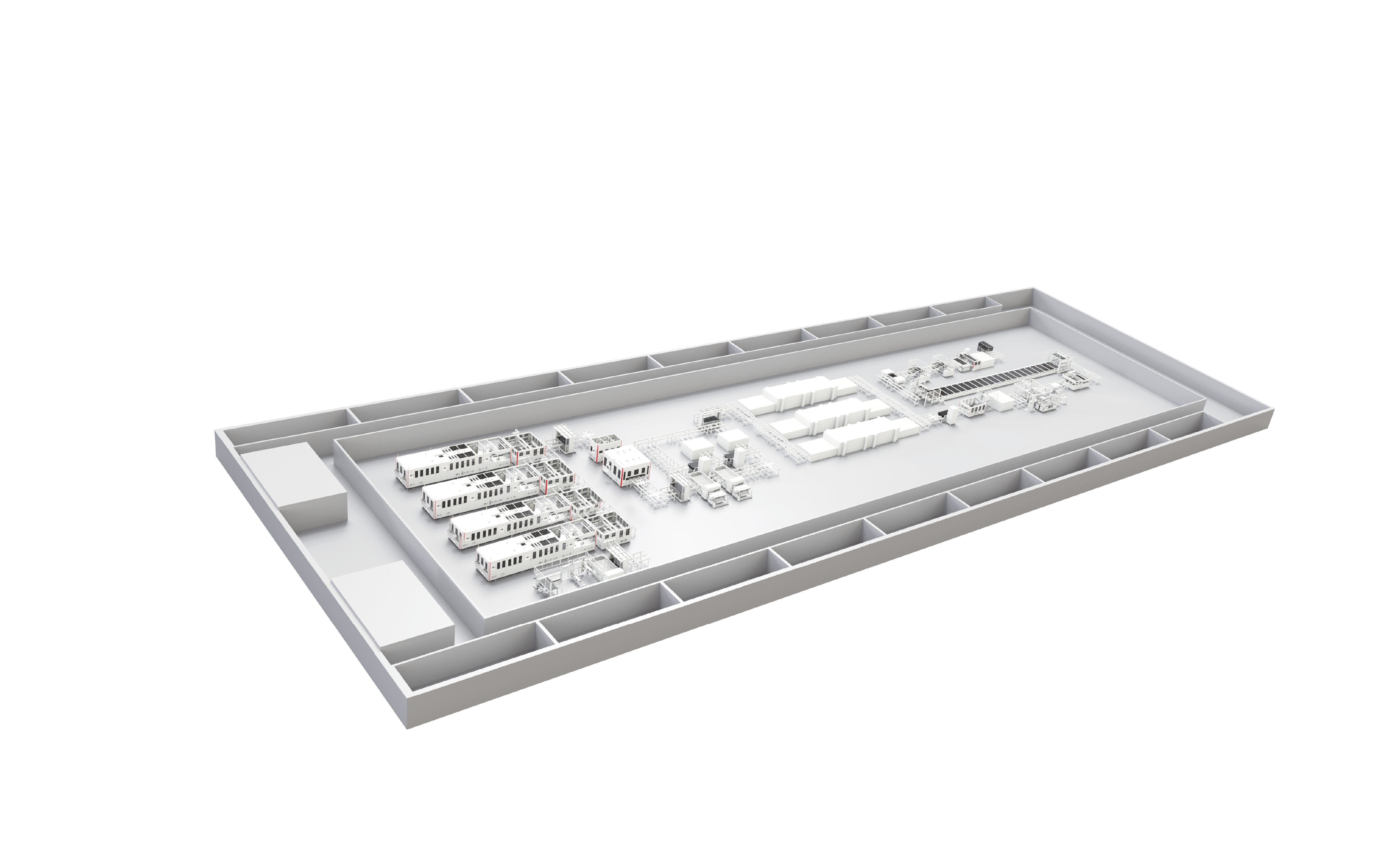
As a leading overall solution provider of intelligent manufacture in the global PV industry, LEAD always adheres to the concept of innovation, constantly upgrades and makes breakthroughs with the most advanced technologies, which promotes to move towards Industrial Era 4.0. LEAD provides PV module stringers, screen printing shingling stringers, Half-cell bussing machine and cell production line turnkey solutions, meanwhile, it has in-depth layout of TOPCon/XBC/HJT/perovskite and other PV intelligent manufacturing solutions, and keeps R&D for the next potential generation of PV Technology . Currently, LEAD has established strategic partnerships with Top-ranked PV companies.
LEAD provides customers with customized solutions, ensures quick responses to customers’ necessity, and help each customer achieve target production capacity in a short time. We provide different types of stringers: stringers integrated with laser cutting, XBC stringers, and 0BB stringers, compatiple with different processes such as TOPCon,XBC and HJT. At the same time, LEAD developed the industry’s first intelligent solution for GW-level TOPCon production with Eta≥26.5%, which makes a TOPCon smart factory with high efficiency. Combined with the self-developed MES system, production data can be inspected throughout the life cycle, which helps achieve an efficient management.