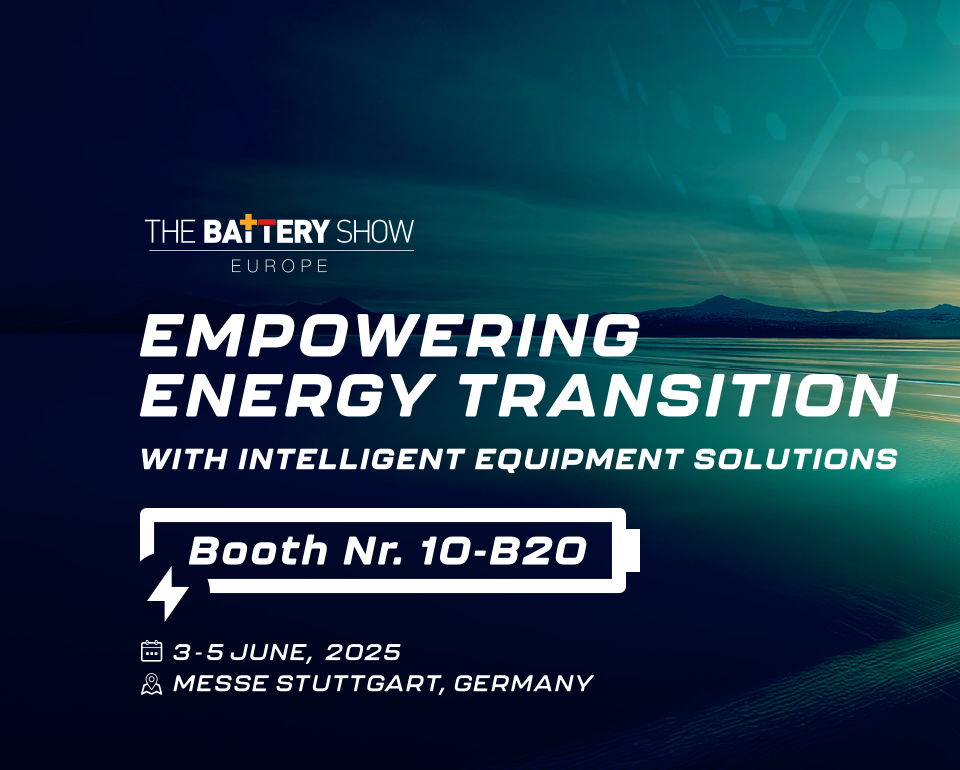
Solutions for Lithium-ion Battery Whole Line Logistics
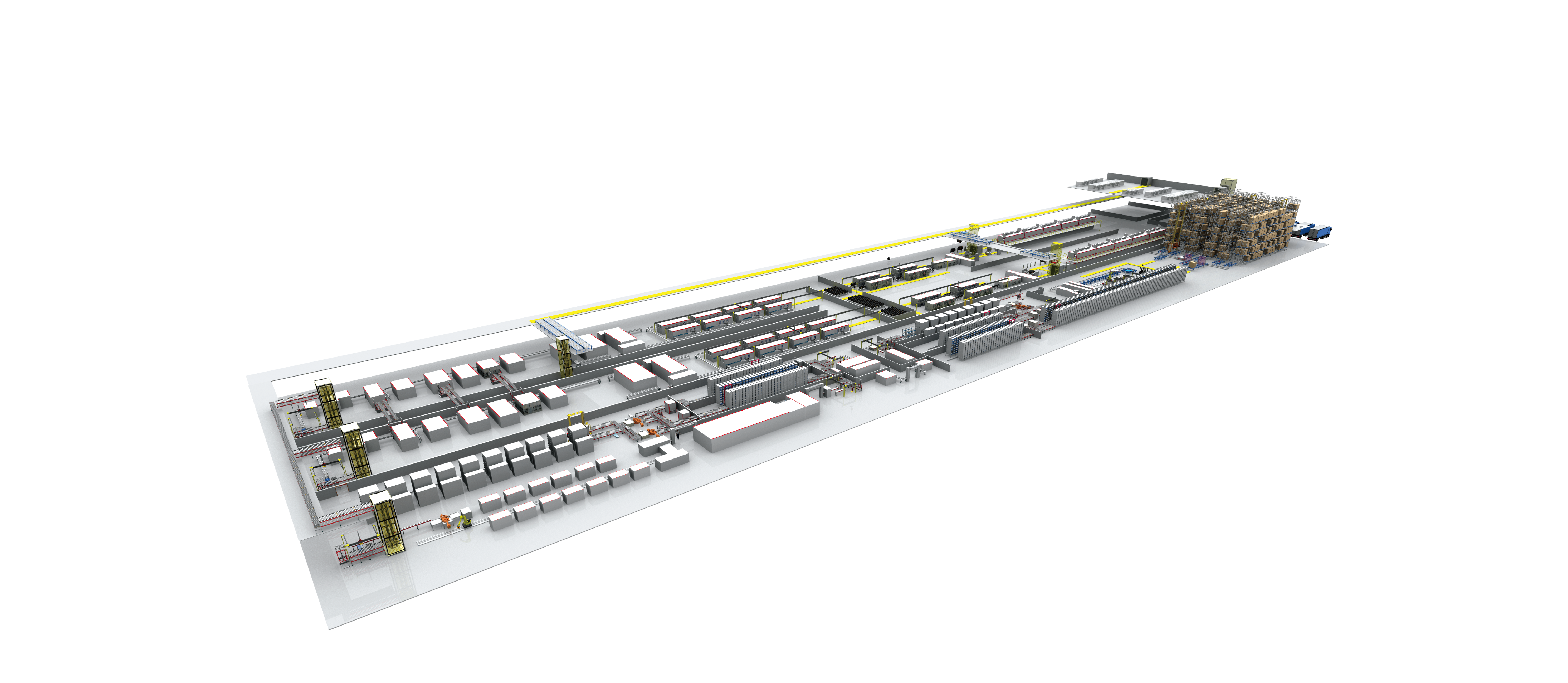
Focused on the new energy production line, LEAD provides full scenario and full process digital intelligent logistics solutions for intelligent manufacturing. It has over 120 cell production lines and has gained orders worth 100Gwh. The solutions for Lithium-ion battery full-line logistics include logistics of upstream raw material warehouses, workshop electrode warehouses, battery cell segments, latter stage of formation and capacity grading, as well as logistics of finished product warehouses and modules and packs.
The company provides solutions for Lithium-ion battery full-line logistics and warehousing, realizing end-to-end unmanned operation and flexible logistics flow with intelligent logistics
equipment. It has built a digital system for the entire factory, reducing carbon emissions by 3.5 billion tons, as an effort to build a zero carbon factory.
Besides, the solutions cover all cell processes (including prismatic cells, pouch cells, cylindrical cells, Sodium ion batteries, solid state batteries, etc.).
Compared to conventional logistics production lines, LEAD has, through intelligent manufacturing and digital logistics, reduced comprehensive human efficiency costs by 30% and increased the automation rate by 50%, reducing the difficulty of management decision-making and solution deployment costs.